How to Reduce Inventory Waste in Your Supply Chain
Inventory waste can be a real bummer. With ever-increasing international competition, price pressures due to uncertainty in the economy and just the good old drive to reduce costs to make the company that much more profitable, suppliers, manufacturers and distributors everywhere are looking into every nook and cranny of their operations, including every link in the supply chain, for cost savings.
But, while reducing costs through faster, more efficient transportation, (especially last-mile delivery), and more effective warehousing and supply chain logistics often come under the microscope, many companies are failing to tap one key area full of opportunities to improve processes and reduce wastage.
Inventory tends to be taken for granted. Your numbers show you need so many raw materials, you have so much work-in-process and you need to stock so many finished goods. All of them include raw materials and the more of each one you have, the higher the chance of wastage at some point in the chain.
But inventory reduction is just one way to reduce waste inventory. Below are just a few more that any lean manufacturing process and supply chain optimization program should consider.
1. Product Design
Whether it’s in the aesthetics or the performance specifications of a finished product and each of its component parts, the design process must always include an assessment to determine if the minimum amount of the least expensive raw material is being used to meet specifications.
Of course, least expensive must be assessed considering all costs, including the materials wastage due to using inferior quality products.
Another option is to review each component to determine if it can be made or sourced for less cost.
2. Production Processes
Each process that materials go through at each link in the chain must be examined with a focus on reducing inventory waste. If a process wastes materials, whether or not they can be recycled, it should be reviewed to reduce or even eliminate the waste.
3. Quality Control
As we alluded to above, the finished quality of inventory stock can effect the amount of waste produced. While you may have found inexpensive raw materials and/or leaner manufacturing processes, is the sacrifice worth more production quality issues, defects, customer service calls and product returns?
Even if a QA reject or customer return can be recycled, there is still a relatively high cost of doing so.
4. Product Packaging
Similar to using lower cost materials, there is a point of diminishing returns when you reduce packaging. But when you add up the cost of buying, handling and shipping excess packaging, the savings you can find by eliminating the excess can be more than worthwhile.
5. Transportation Transformation
If your products get to your customers a moment too soon, or a moment too late, you’ll experience some sort of inventory wastage. Similarly, every moment one of your loaded trucks spends inactive at a loading dock can be considered inventory waste. Always review transportation times and costs at every stage of the supply chain.
6. Over-Processing / Over-Handling
Any processes your products go through that don’t change its value, either through increased functionality, better appearance or speed to market, can result in inventory waste, even if that’s just from having the inventory in your hands for longer than needed.
There are many more ways you can experience inventory waste throughout the supply chain. One of the best overall as to reduce the waste is to increase your inventory visibility as much as possible, including through up-to-date inventory management systems, at every step of the process.
To learn more about reducing your inventory waste and optimizing your entire supply chain, check out our warehousing services and give us a call to find out which solution is right for you.
Stay Up-To-Date
There's always something new from PiVAL
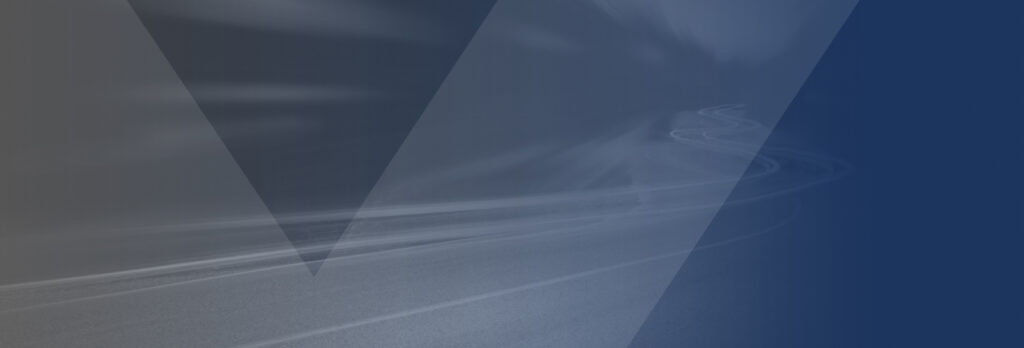
Comments are closed.